Laser Welding is a superior technology for welding defects in any type of tooling, plastic injection molds, stamping dies, blow molds, turbine blades, and nearly any tooling component made of stainless steel, aluminum, copper alloy, cast iron, and all tool steels. Now, pulsed laser welding is being utilized to repair 3D printed parts as well.
3D printed parts, also known as Additive Manufacturing, have made fast inroads in the tooling industry. In the plastic injection mold industry, the speed of cooling is a critical factor in how fast the mold will cycle. With the introduction of 3D printed parts, engineers are now able to move water lines closer to the molding surfaces to cool the plastic faster so the molded part can be ejected faster. This innovation has reduced cycle times significantly and has increased the output of each mold.
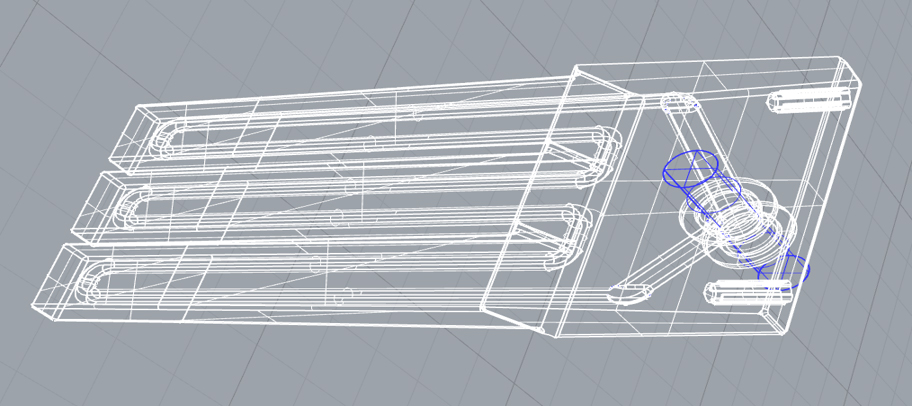
This new tooling made with Additive Manufacturing is printed layer by layer and designed with conformal cooling. Unfortunately, the thin sections and hollow areas of these 3D parts are more prone to warping, cracking, and other damage when traditional welders are used for repair. Laser welding has become the go-to repair method for these tooling parts because of its low heat input.
Laser welders offer precise control and little heat input
A pulsed laser beam can precisely control how much heat is introduced into the workpiece. A laser welded Heat Affected Zone is only .004 -.010 deep and the workpiece is softened in that shallow HAZ by 2-4 points on the Rockwell scale. With a conventional welder, the HAZ would be .100 deep or more and the workpiece would be softened by 15-22 Rockwell.
Physics 101 tells us that heat drives grain growth and when grain size grows it becomes weaker. Therefore, heat is not your friend when welding tool steels. The pulsed laser welder introduces so little heat into the workpiece that a bare hand can be laid on the workpiece when finished welding and the color of the workpiece never changes. And that welded part can be finished machined immediately.
Additionally, the TIG welder may have difficulty reaching certain areas on the part, especially at the delicate edges. Unlike the torch of a TIG welder, the beam of a laser welder shoots straight out from the machine and doesn’t obstruct the tech’s view – as long as the tech can see the area to be welded, it will be welded. A TIG welder simply doesn’t have that flexibility or precision.
Laser welding speed is catching up with TIG welding
The newest generation of laser welders are significantly faster than just a few years ago and are approaching the speeds of TIG welding. Yet with the laser, heat input into the part is managed much more efficiently – controlling for thermal growth, distortion, warping, and annealing. Laser welding more accurately applies metal to the defect area, but stays off adjacent surfaces, greatly reducing rework times.
The cost of 3D printed parts is considerably higher than parts manufactured by traditional methods. That makes laser welding a cost effective choice for repairing a damaged part. Instead of scrapping a damaged or misprinted part, the pulsed laser welder can repair it effectively with little damage, regardless of the materials the part is made from. Pulsed laser welding creates extremely low dilution, so that the base metal and the welded materials are bonded, but not forced to dilute, eliminating porosity or cracking.
Laser welding is an outstanding solution to many of the manufacturing problems confronting the Additive Manufacturing industry. It can be used to join many uncommon alloys, can be deployed in areas of parts with delicate details and features and causes very little damage or change in the base substrate.
Most of the lasers sold by Alpha Laser are capable of welding 3D Printed Parts. See our laser welders here.