In nuclear power generation, a turbine shaft is a key piece of equipment. Without it, there would be no way to drive the turbines that create electricity. It’s the essential link between the steam produced by the fission reaction and the electricity that lights a city.
Which is why a nuclear plant operator was alarmed to find nicks in a brand new turbine shaft scheduled for installation.
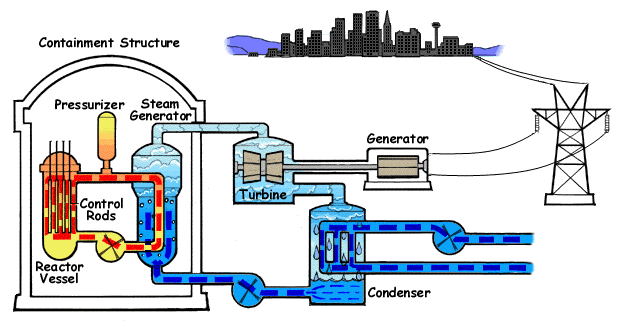
Nicks may sound like a small deal to the average man on the street, but to the operator of a nuclear power plant, it’s the difference between a shaft which rotates the turbine reliably year after year or a county-wide blackout when it cracks or fails. That’s because a shaft in a nuclear power plant must be perfectly within spec so that when it rotates, force is distributed evenly across the shaft. But nicks cause inconsistencies in the rotation which places stress on the metal, which may eventually cause it to crack. And even minuscule cracks introduce more weakness into the metal and more inconsistencies in rotation, causing more cracks. And so on.
This particular nuclear power plant shaft was made of an incredibly dense austenitic nickel-chromium superalloy called Inconel, specifically developed for service in extreme environments with high pressure and kinetic energy. It’s more durable under heat than steel or aluminum, yet inconsistencies appear in the manufacturing process which are difficult to machine off.
It was during an inspection of the shaft in the machining process that nicks were discovered, and an inquiry call was placed to Alpha Laser.
Laser welding vs TIG welding when precision matters.
Nicks in any metal, even the hardest alloy, can be removed by welding. The problem with traditional or TIG welding is that it does a lot of damage to the metal and reduces the hardness (Rockwell scale) in the heat affected zone (the area in and around where the weld took place). So while the metal at the welds doesn’t appear to be damaged, it’s actually softer than the areas that weren’t welded, making the shaft weaker at those points.
Because of the precise nature of laser welding, no weakening occurs at the welded areas, as the heat affected zone is smaller and cools instantly. TIG welding is also very imprecise and creates a much larger buildup of material on the metal surface than with laser welding. This buildup has to be machined off to the thousandths of an inch. So laser welding also creates less work for the machine shop.
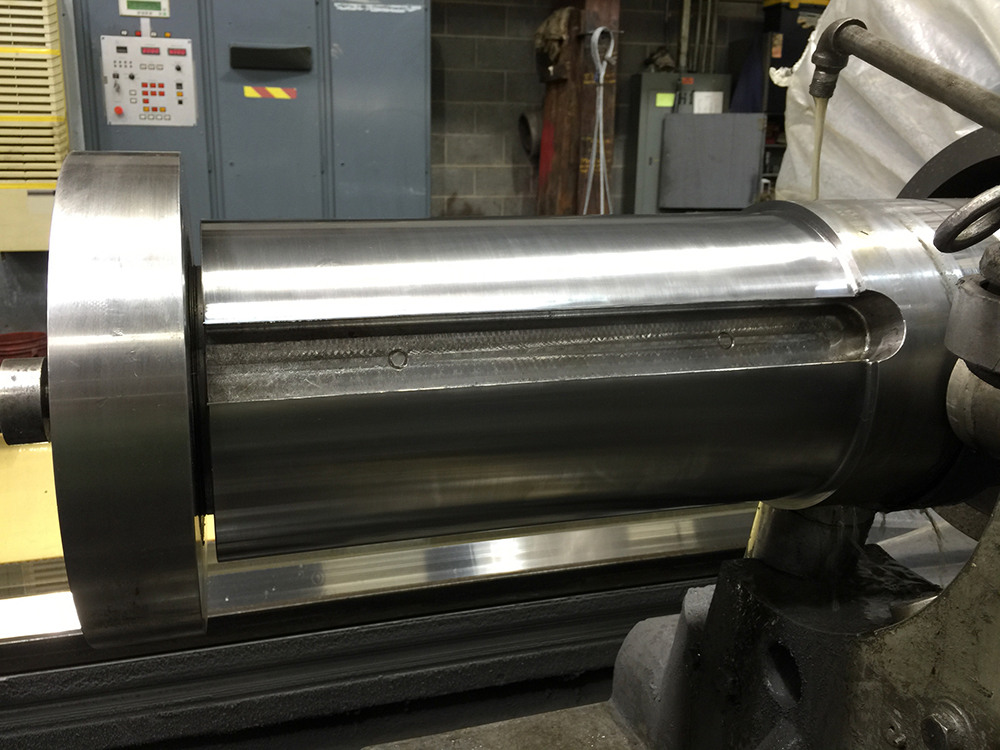
Laser welding the turbine shaft.
Confident that laser welding was the way to go, the nuclear plant operator shipped the 20,000-pound shaft to Alpha Laser, where the laser welding took place.
Because they needed mobility and power to weld a 20,000-pound shaft of an extremely dense nickel alloy that was 15 feet long and ranged between 11 inches and 6 feet in diameter, Alpha Laser rigged up a powerful 500 Watt Nd:YAG laser to the Alflak mobile laser. This not only was very effective in welding the damaged areas but also was flexible enough to easily reach any spot on the shaft.
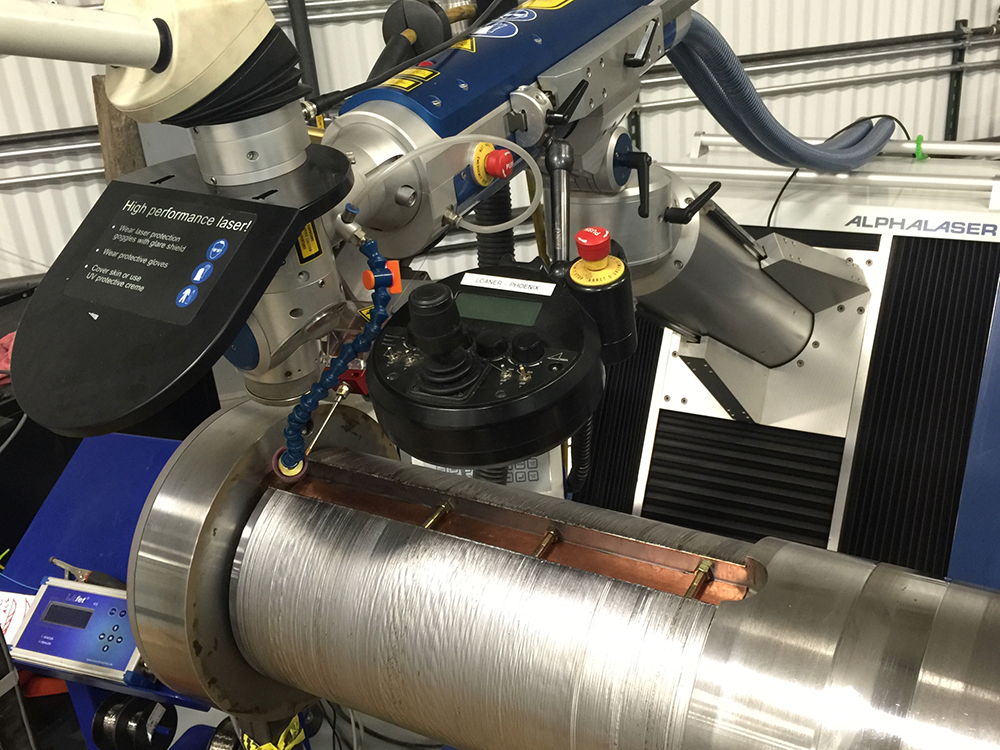
Alpha Laser spent 5 days repairing the nicks. As time was a major consideration for the plant operator, when Alpha Laser’s work was done in Pennsylvania, they accompanied the shaft to a machine shop where the finishing took place. Alpha was on hand so that any new inconsistencies could be quickly repaired and machined.
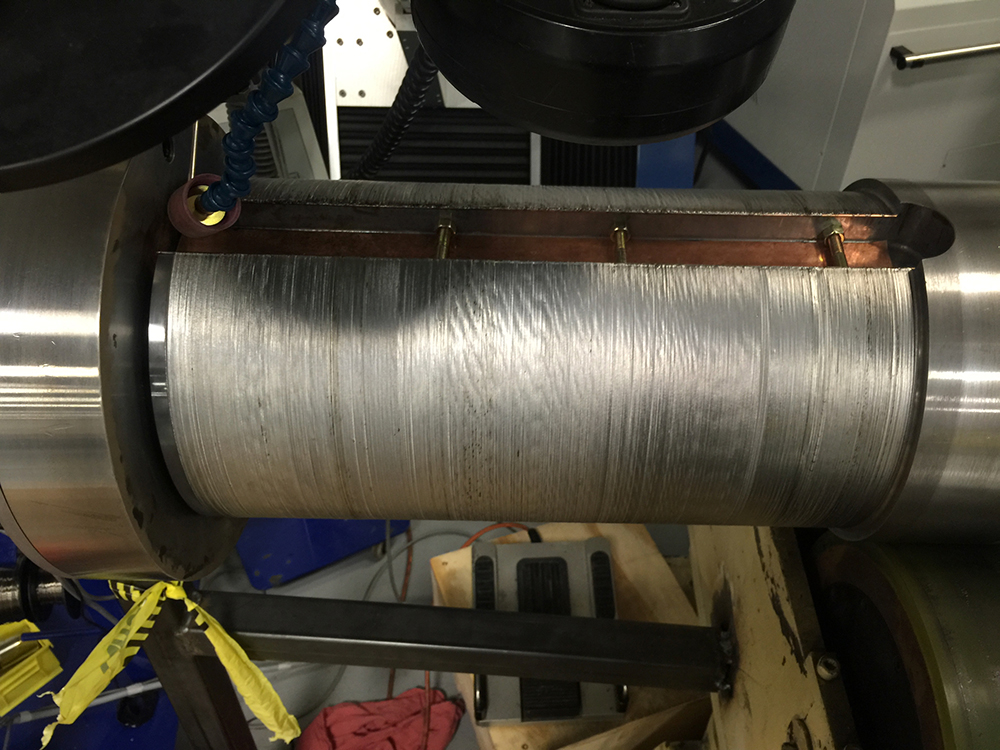
Total turnaround time for the shaft repair was 20 days, including shipping, repair, and machining. If the shaft would have been returned to the manufacturer and a new one made, downtime at the plant may have been up to 20 weeks, not days.
Laser welding was clearly the superior choice.
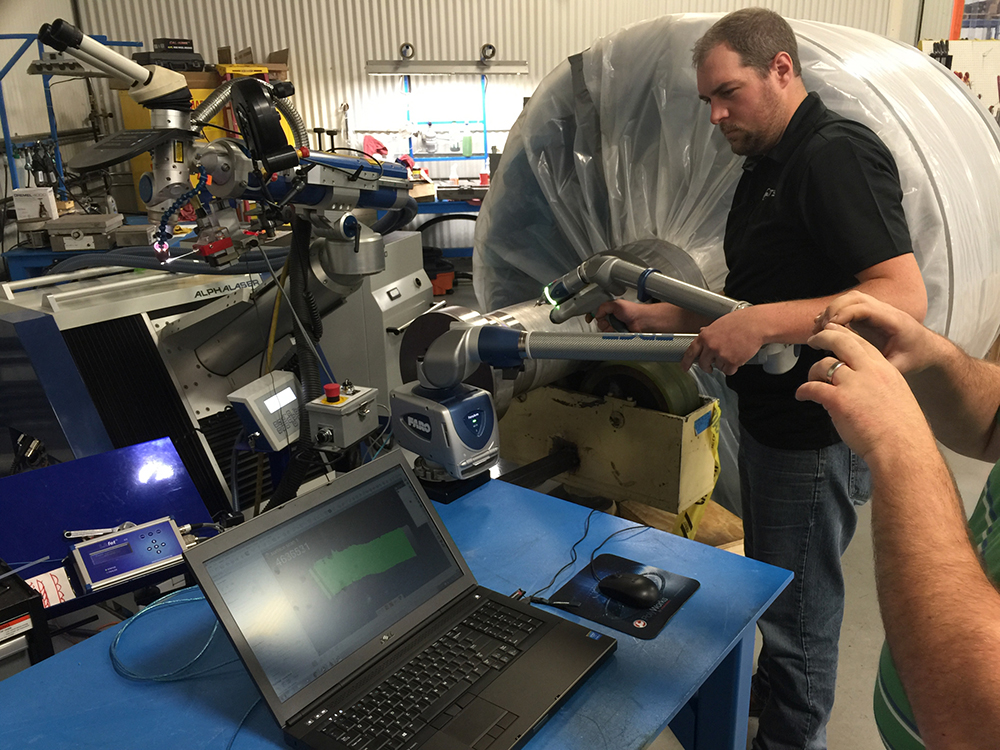